For more than half a century waste plastics and rubber have been clogging the landfills, filling up the oceans, and littering the side of the roads on the entire planet Earth. Now, there is waste plastic recycling equipment that can alleviate the millions of tons of waste and convert the plastic into usable products like oils, gas, carbon black, and other commodities. Not only that, but many of these plants can be made self-sustainable so that they use some of the recovered oils or gas to run on, thus eliminating a huge cost factor as well. There are several important design considerations that have been introduced in these pyrolysis plants in recent years, here are just a few.
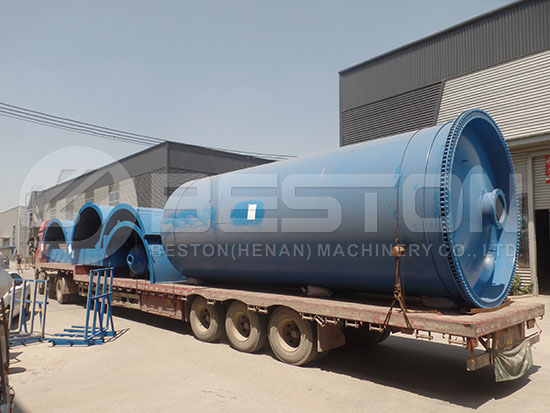
Key To Waste Pyrolysis Plant
One of the first things that a newcomer to the pyrolysis process will say is that burning plastics and rubber create poisonous and toxic fumes. However, the only time that there are any toxins released would be if the recyclables are burned, which is a chemical reaction involving oxygen. But, by restricting the oxygen, the plastics can be superheated, they won’t catch fire, but will break down into basic components like oils, gases, and carbon. Thus it can be called waste plastic to oil plant. It can be used to recycle waste tire, namely tire oil plant.
The most important other consideration is that, because nearly all plastics can be run through the same plant, no sorting needs to take place. The thousands of man-hours spent in the past separating the various grades and types of plastics is over. Most plastics couldn’t be recycled in a typical way because once heated they couldn’t be reformed into a usable product. With a pyrolysis reactor, on the other hand, they are broken down into very basic components instead.
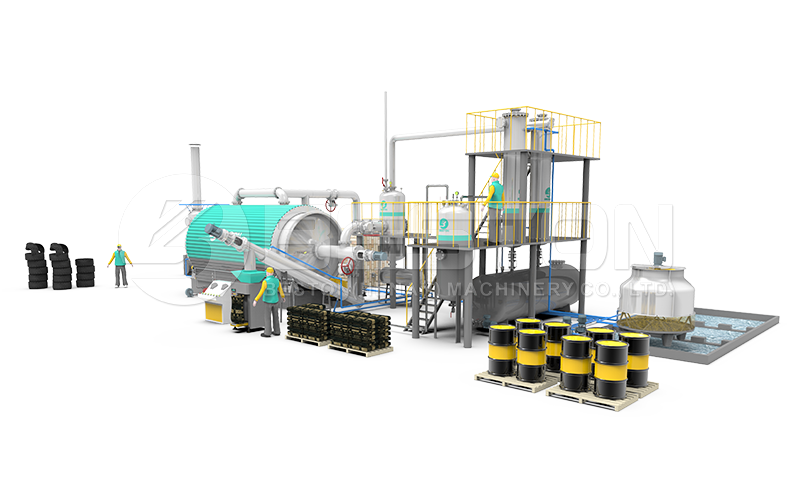
The New Pyrolysis Plant Designs Come In All Sizes
These waste plastic pyrolysis plants are usually rated by the number of tons of materials that they can process every day. Some plants will process 6 tons per day while larger plants can do 50 tons per day. It all depends on how much material is coming into the recycling plant. Some municipalities have great recycling programs that will gather nearly all the plastics available in a huge geographic area and this is better for the environment.
Some plants are made to just run batches and then shut down and wait for the next batch. Other plants have a continuous conveyor belt that is constantly running all day every day. Large cities may sometimes use several plants, one for tires, another for plastics, one for waste oils and even one for wood or agricultural waste as well. Each plant may have different operating temperatures that are carefully chosen for the best results for the type of waste they consume.